Torque motor is a term that has been created to describe a motor that will be used mainly for torque control in a precision system. Many of these systems move in very small increments and limited angles of rotation and the motor could be holding position against a varying load. That doesn’t mean that torque motors cannot run at high speeds, in fact many of them do. Torque motors are also typically frameless kits consisting of a rotor and a stator that the user integrates into other mechanical systems.
The frameless torque motor is essentially the magnetic guts of a traditional motor without a shaft, bearings or housing. Below is a good example, key features of low axial profile, large internal through hole, and thin radial cross section.
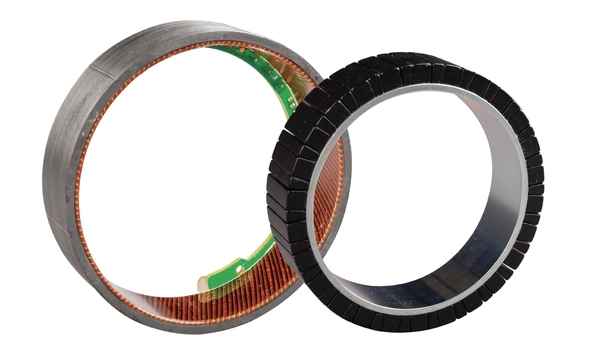
TORQUE MOTOR APPLICATIONS
Torque motor applications include gimbals, rotary turrets, indexers, precision rotary stages and any application where movement is precise and torque control is the dominant application requirement, (as opposed to speed control). Many of these systems are also direct drive applications where smoothness of torque production with angle is critical. In some applications like robot joints, torque motors are used in combination with a high ratio zero backlash gear to create high torque in a very low axial profile. The above motor is a slotless motor with zero cogging torque and really optimized for direct drive applications.
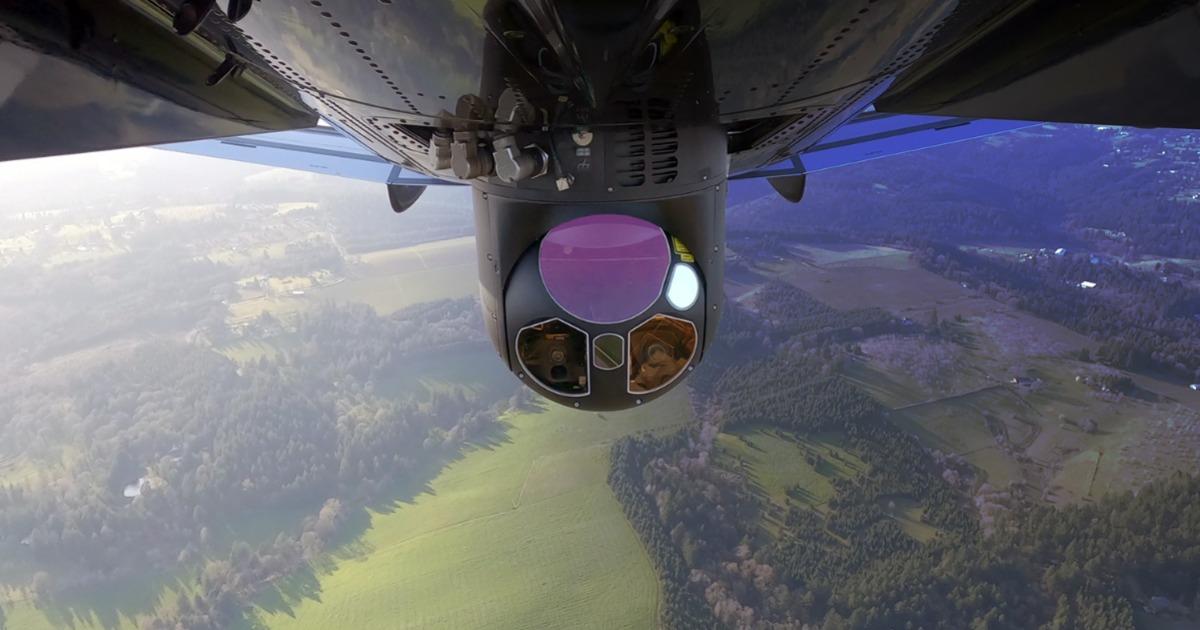
Torque Motors for Camera Gimbals
Most motors, even well-designed frameless torque motors, still have torque ripple when operating at near zero speed. Magnetic design choices have been made in the iron, copper, and magnets to get a reasonable compromise between thermally limited torque output, motor constant, and mechanical size. Unfortunately, this compromise results in cogging and non-linear torque output with current.
The best design for optimum torque control is a motor that has very sinusoidal torque production with angle and zero cogging. Sinusoidal torque production works in harmony with sinusoidal current waveforms from the motor driver to create a smoothly rotating torque vector. Slotless motors like the picture above are the best at producing both sinusoidal torque output with angle and zero cogging. All other technologies tend to have higher harmonic content, cogging, and saturation at higher current levels. All these limitations impact smoothness and create torque ripple.
BRUSHLESS DC TORQUE MOTOR
The torque motor is a specific magnetic version of a brushless DC motor (Synchronous motor). It is larger in diameter than it is in axial length. The pole count is generally high >10 and as high as 100. With a high pole count the peak efficiency point of the motor occurs at a lower mechanical rotational speed. This higher pole count and larger diameter motor combination optimizes torque production at the expense of high inertia and generally lower speeds, (determined by the limits of the control system and the higher electrical driving frequency required). Another differentiating point is the thin radial cross section with large through hole in the rotor that most torque motors have.
BACKGROUND INFORMATION ON MOTORS
DC motors are more commonly identified with variable torque or controlled torque applications. Current flowing in a DC motor directly relates to torque output. The motor does not need to be moving for this phenomenon to happen. Because of the evolution of motors and their uses starting with Speed as the dominant factor, original DC motors took on a form factor similar to AC Induction motors and more easily adapted to variable speed requirements because torque was proportional to current and speed was proportional to voltage.
Short axial length and large diameter motors were created for lower speed low acceleration direct drive applications. Diameter was used to get higher torque, because motor torque output increases with diameter faster than it increases with length. Higher pole counts allowed for thinner lamination thickness by localizing magnetic field paths. Higher pole count motors generally create more torque in the same package. Motor inertia also increased but these direct torque drive typically did not need high acceleration.
The ability to control torque output without moving suddenly enabled many new applications where a motor could be used as a torque device and didn’t have to rotate. Tensioning, winding, haptic torque feedback was all possible with the DC motor. This was not possible with an AC Induction motor without significant excess heating and the controls that were not available until almost the end of the 20th century.
During the computer revolution, electronic controls with transistors and microcontrollers could accurately control current in multiple phases. Brushes and commutators were removed from DC motors and replaced with position sensors and transistors. Brushless DC motors (AKA Synchronous) were enabled and became widely available. Suddenly new form factors became available for the DC (now brushless) motor.