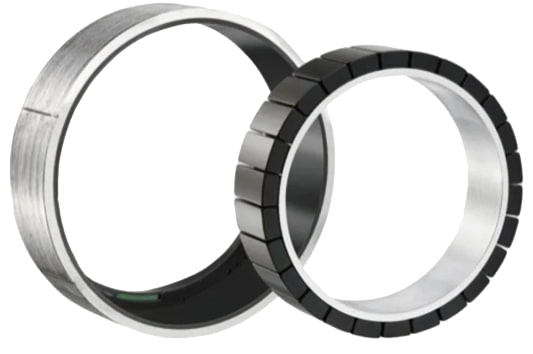
Motors designed for direct drive operation tend to be large in diameter with a high pole count (>10 poles). The axial length is short and a large through hole aperture is common. Sierramotion designs to the application optimizing the number of poles in the rotor. Then the proper stator is selected which could be a traditional iron based stator for the highest torque output or a slotless air-core stator for optimum smoothness.
Large diameter and low axial profile form factor
Direct drive applications always benefit from large diameter and higher pole counts. Maximizing the diameter of a motor provides the highest torque output because torque increases with radius and cross sectional area for copper increases by the square of diameter.
Thermal optimization
Design for high thermal conductivity is accomplished by encapsulating the winding with a thermally conductive epoxy. Designing for convection and air cooling exposes motor wiring to airflow. Vacuum applications require good mechanical bond to the housing for optimum conduction.
Optimized winding parameters
Connect to low voltage (12-24), medium (48-100) or high voltage (300-600). It is just a winding scaling away. It is even possible to optimize for an obscure voltage like 19 or 39. Don’t accept sub-par performance, match the motor controller and application to get the most out of your direct drive project.
Modular Contruction
When it comes to large diameters, designing and building the motor to be modular can save on shipping and other costs. Arc-shaped motor components will then be mounted into the final assembly and become a complete motor.
Direct Drive Motor specifications
Specifications | |
---|---|
Low Speed | Speeds below 1 rpm are typical |
Torque Control | Zero speed torque control |
High Speed | Up to 30,000 rpm |
Air Bearing Integration | Motor optimized to work with Air Bearing |
Encapsulated Stator | Fully potted stator thermally conductive epoxy |
Surface PM rotor or IPD | Optimized for torque or speed |
Vacuum rated | Fully enclosed rotor and stator in stainless steel for deep vacuum or space |
Frequently asked questions
Generally direct drive motors are larger in diameter than length and have high pole counts. This can make them have higher torque than a traditional long small diameter motor. Torque output increases with diameter faster than with length
Absolutely not. The old days of using a coupling between the motor and the load prompted this limitation, it had nothing to do with the motor and everything to do with the coupling.
Yes, most direct drive motors have a large through hole that can be used for running wires or optics. The center of any motor is normally not used, except for a shaft to connect to a coupling both of which are no longer there with this type of motor application.
Yes, as long as they are electrical wound to do so. Originally high pole count motors could not run at high speed due to controller limitations, but today’s controllers have no issue with high pole count motors and higher driving frequencies.
Stiffness of a motor like this is directly related to the encoder used. If a high resolution encoder is used the stiffness can be very high.
Yes. However, response is related to torque available and inertia. Direct drive motors tend to have higher inertia than traditional motors making their acceleration less. If the direct drive motor is connected to a load that has much higher inertia (typically the case) then the response may be better than a traditional motor connected through a gear box and coupling in order to handle the higher inertia.