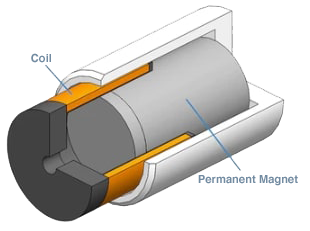
Voice coil motors evolved through the original audio speaker design. The voice coil was used to vibrate the speaker cone and create sound waves. Modern day voice coil motors (VCM) can be found in many precision systems that have limited travel. The motor consists of a cylindrical magnet and cylindrical coil that are coaxially mounted. Applying current to the coil creates a force in the axial direction. The coil or the magnet can move depending on which is held fixed. VCMs are scale from small sizes of < 10 mm diameter to larger sizes up to 1 meter or more in diameter. They typically travel less than 10 mm.
Optional sizes from 10mm to 1000mm diameter
This simple construction allows them to be built to order. No precision tooling is required to make motor parts. It is as simple as a magnet and coil.
Optimized mounting configurations
The two parts (coil assembly and magnet) are totally configurable and can include mounting features. If the coil moves a flex circuit is usually required. If the magnet moves, its mass needs to be considered along with the load to insure acceleration is possible.
Controlled Force
The primary result of flowing current in the winding will be a force. The force output is very linear with current. Force production tends to vary with position, where an optimum position is at the center of travel. Therefore, it is important the make sure the control system and servo tuning loops can handle a changing force constant with position. The VCM travel is usually limited to a range that has reasonable force output.
Low or High Voltage
The VCM winding can be configured to operate down to 5 volt and as high as 600 volts (while this may not be practical based on the size of the VCM).
Position with a voice coil motor (VCM)
A VCM can be assembled on to a bearing system that can be mechanical, air bearing, fluid bearing, or a flexure. Once the VCM is suspended and can move, and encoder can be mounted to the assembly. Resolutions as small as 10 nanometers are possible with modern encoders. Accuracies to less than 1 micron are also possible.
Speed of voice coil motors
If the coil is moving, they can move very fast. This requires some type of flex circuit. Any system can only accelerate at a rate proportional to the force developed and the mass of the moving system. Moving an optical lens is a good example where it may only weigh a few grams. The VMC is an excellent choice for this and with proper design the lens can be in the center aperture of the VCM.
Voice Coil Motor specifications
Sierramotion voice coil motors are customized to the application. Whether moving coil or moving magnet options are chosen, the size and force ranges, as well as the voltage and current can be adjusted to suit the need. Precision force control is possible and special high force bucking magnet versions are also available.
Specifications | |
---|---|
Diameter range | 8mm to 2000mm |
Axial length range | 5mm to 400mm |
Voltage operation | 5 volts to 600 volts |
Temperature range | -50°C to +70°C (with option for 200°C+) |
Vacuum rating | Down to < 9E-9 with proper design |
Radiation hardening | Using laser welded cover |
Torque output | .01 to 1000 NM |
Speed ranges | .0001 rpm to 5000 rpm |
Frequently asked questions
The VCM is a two wire device, it can be controlled with a DC drive or a DC servo drive.
Most VCMs are limited to <25mm in travel because the device is typically single phase (two wire). Longer travels are possible with multi-phase (2 or 3 ) devices. It is possible that a tubular linear motor or a linear motor may be the better solution in this case.
The tubular linear motor is a mult-phase version of voice coil motor with a moving magnet assembly. In a VCM either the coil can move or the magnet can move. Most units use the moving coil for high response but it requires that the wires move and usually requires a flex circuit.
Yes, definitely, the design is perfect for force control if a force sensor is used as the feedback force resolution down to .01 Newtons is possible.
Yes, as long as the magnetic encoder scale moves along with the motor magnets. The issue that can impact operation is if the motor magnet doesn’t move and the magnetic encoder scale (also a magnet) is moving. The motor fields can interact with the encoder sensor. If this is the case, then an optical, inductive, or capacitive encoder is a better option.